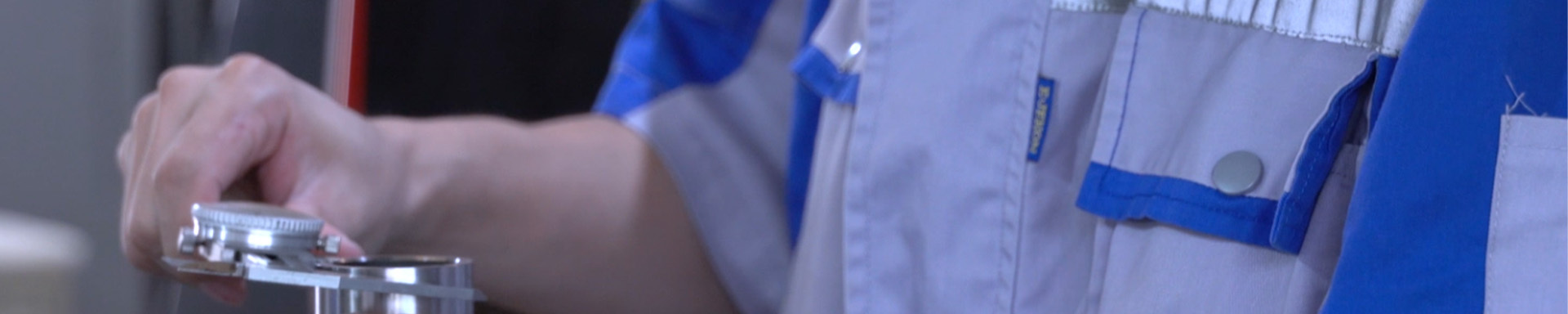
- Home
- >
- News
- >
- Industry News
- >
News
Cobalt alloy welding pieces provide outstanding wear and corrosion resistance for centrifugal filters, extending component life, reducing downtime, and ensuring stable operation in harsh industrial environments.
Cobalt-based alloys offer exceptional toughness, corrosion resistance, and wear resistance in cryogenic environments, making them ideal for aerospace, LNG, and superconducting applications.
When machining cobalt alloys, numerous key factors are interrelated and collectively influence the quality and efficiency of the machining process.
Discover how cobalt alloy bushings significantly improve the performance and lifespan of metallurgical valves used in blast furnace systems. Learn about their wear, corrosion, and high-temperature resistance advantages in Qinye's hot air, butterfly, and vent valves.
Discover how cobalt-based T400 valve seats deliver high-temperature and corrosion resistance in industrial generators using biomass fuel. A real-world case from Germany's Onets GmbH highlights the alloy’s superior performance.
In glass wool production, manufacturers must choose perforated disc materials to balance fiber quality and equipment durability. Operating in high-heat factory environments, discs face extreme conditions. Nickel alloys suit slower processes for coarser fibers, while cobalt-based materials are ideal for high-speed setups requiring fine filaments.
In metalworking, flash butt welding’s post-weld flanging treatment struggles with traditional inefficiencies. Cobalt-based alloys serve as slag scrapers, offering wear resistance, high-temperature stability, and electrode compatibility.
Steam turbine blades operate in extreme environments with high temperatures, corrosive media, and mechanical stresses. Over time, corrosion and wear degrade blade performance, leading to efficiency losses and costly maintenance. To address these challenges, Alloy 6B/UNS R30016 is a superior material for wear strips and protective overlays on steam turbine blades. This cobalt-chromium-tungsten alloy complies with AMS 5894, combining unmatched corrosion resistance, high-temperature stability, and mechanical durability. This article explores the root causes of turbine blade corrosion and the criteria for material selection.