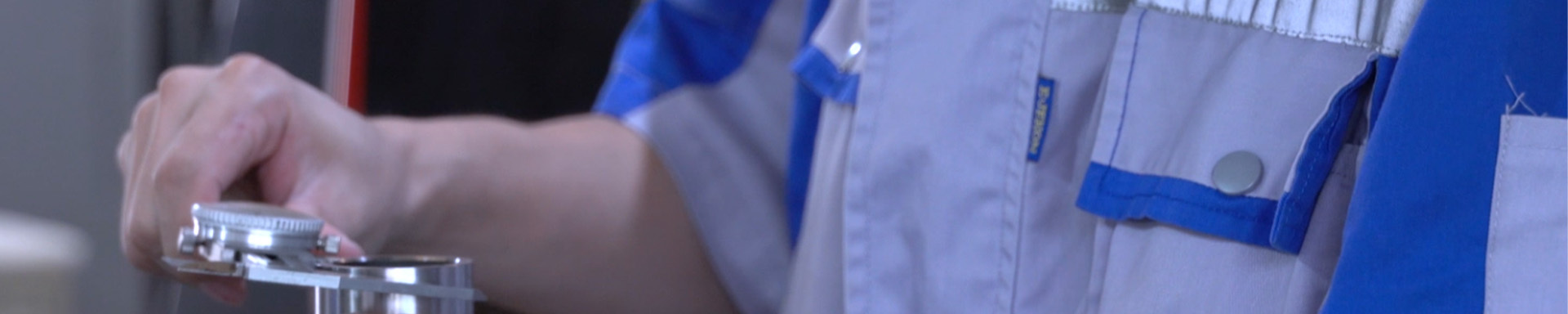
Cobalt Alloy Applications in Homogenizers
2025-04-16 09:00Homogenizers are widely used in food, pharmaceutical, chemical and other industries to homogenize materials by physical means such as high-pressure shearing and impact. The performance of its core components directly determines the equipment's life and operational efficiency; cobalt alloy has become the core material of the homogenizer's key parts by its unique wear resistance, corrosion resistance, and high-temperature stability.
The Core Application of Cobalt Alloy in Homogenizer Parts
Valve Seat and Valve Plug
The homogenizer's valve seat and plug need to withstand high-pressure impact and material friction for a long time. The hardness of Alloy 20 can be up to HRC 56-60, and the high hardness and abrasion resistance conferred by its carbide phase can effectively resist the wear of high stress and extend the life of parts. In the food industry, these fittings must be frequently contacted with acidic fruit juice or enzyme-containing dairy products. The alloy's corrosion resistance can avoid metal ion migration and ensure food safety.
Homogenizing Valves
Homogenizing valves are the core component of high pressure homogenizers and are designed to withstand extreme pressures (often in excess of 1,000 bar) and high fluid velocities. Homogenizing valves made of cobalt alloys (e.g., W-valve, wave-valve combinations) are optimized to enhance fluid shear efficiency and reduce energy consumption while maintaining a low surface roughness and reducing material residue. For example, in emulsification systems, the secondary homogenizing valve significantly improves product stability by controlling the uniformity of particle distribution.
Plungers and Sealing Components
Plungers for homogenizers need to be both strong and wear-resistant. The metallurgical bonding layer formed by surface welding or spraying technology (such as plasma cladding) of cobalt alloy can resist long-term reciprocating friction, and its high-temperature stability (≤480℃) can prevent seal failure and ensure airtightness in high-pressure environments.
Core Performance Advantages of Cobalt Alloys
Excellent Wear and Corrosion Resistance
The carbides formed by chromium, tungsten, and other elements in cobalt alloys resist abrasive wear and chemical corrosion. For example, the dense oxide film (Cr₂O₃) generated by chromium can isolate acidic and alkaline media, which is particularly outstanding in the petrochemical industry in the treatment of high-viscosity materials containing particles.
High-Temperature Stability and Mechanical Strength
Cobalt alloys maintain their high strength and creep resistance at high temperatures, where localized friction can cause temperatures to soar above 480°C during homogenizer operation. Its low coefficient of thermal expansion ensures dimensional stability under high-temperature conditions, avoiding seal leakage due to thermal deformation.
Biocompatibility and Processability
Cobalt alloys are free of toxic elements (e.g. lead, cadmium) and have a high surface finish, which meets the hygienic standards of the food and pharmaceutical industries. In addition, it can be processed through casting, cladding, laser cladding and other processes to meet the needs of different working conditions. For example, plasma cladding technology can realize the preparation of nanoscale dense coating on the surface of the valve seat to improve wear resistance.
Industry Applications
Food Processing
In the fruit juice homogenization process, cobalt-alloy valve manifolds can run continuously for more than 8,000 hours, which is more than three times longer than traditional stainless steel fittings, and avoids the risk of metal contamination at the same time.
Bio-pharmaceuticals
Homogenizers are used for cell breakage or liposome preparation, and the corrosion resistance of cobalt alloys can resist the erosion of biological enzymes and organic solvents, ensuring the cleanliness and consistency of the production process.
Chemicals & Coatings
When handling coatings containing abrasive particles, the high hardness of cobalt alloys dramatically reduces wear and tear on fittings, minimizing downtime and maintenance.