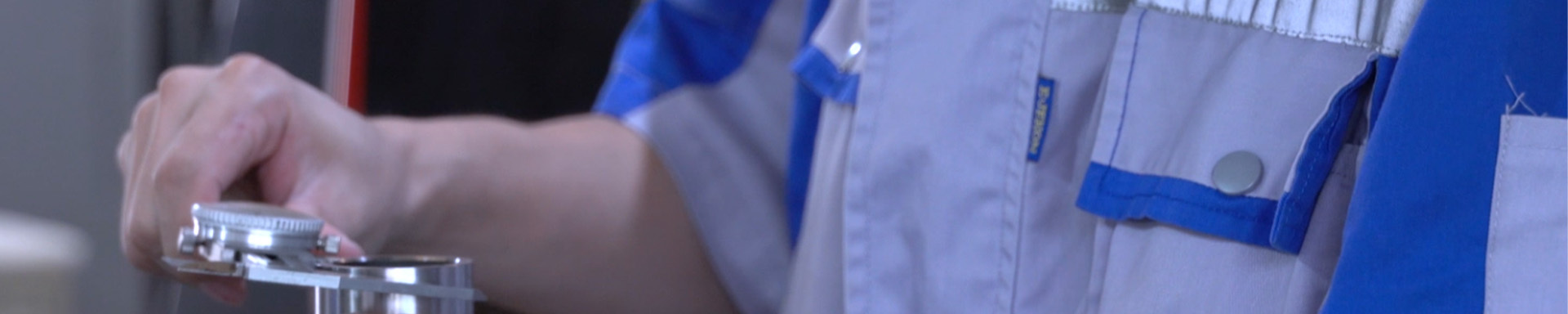
How to Solve the Wear and Corrosion Resistance Challenges of Centrifugal Filters?
2025-07-11 09:00In industrial production, centrifugal filters serve as core equipment for solid-liquid separation, with their operational efficiency and stability directly impacting the production pace and cost control. Especially in the food processing industry, centrifugal filters must withstand severe wear caused by high-speed operation and endure corrosion from acidic and alkaline medium, making the material properties of equipment components critical. Cobalt alloy welding pieces effectively address centrifugal filters' wear and corrosion problems.
Material Performance Challenges for Centrifugal Filters
Centrifugal filters generate centrifugal force through high-speed rotation to achieve solid-liquid separation. Their core components face three significant challenges during operation:
Severe wear: Continuous friction under high-speed rotation leads to component surface degradation.
Corrosion: Contact with materials, especially acidic media in food processing and corrosive liquids in chemical industries, leads to rapid corrosion of components.
Maintenance cost: The equipment requires long-term stable operation, and frequent shutdowns for maintenance significantly increase production costs.
Traditionally, companies have primarily used 440C stainless steel or tungsten carbide as materials for the critical components of centrifugal filters, but the results have been unsatisfactory. 440C stainless steel lacks sufficient corrosion resistance, resulting in a short service life in acidic media and frequent replacements that cause production interruptions. At the same time, tungsten carbide has good wear resistance but lacks toughness and corrosion resistance, and is prone to edge chipping at high speeds, posing a risk of equipment failure.
Cobalt Alloy Welded Pieces
Cobalt alloy welded pieces have solved the problems of centrifugal filters due to their unique performance advantages.
Wear resistance: Cobalt alloy welded pieces can offer excellent wear resistance, especially at high temperatures. The hardness is sufficient to withstand friction and wear during high-speed operation of centrifugal filters.
Toughness: Cobalt alloy's excellent toughness resistance prevents chipping and other issues under impact and vibration, ensuring stable equipment operation.
Corrosion resistance: When exposed to acidic or other corrosive media, cobalt alloys effectively resist corrosion, extending component lifespan and reducing downtime caused by corrosion-related maintenance.
Safety: Cobalt alloy is a safe metallic material that complies with safety standards in industries such as food processing, ensuring it does not contaminate products and maintaining production safety.
Vietnam Kengta Technologies uses its centrifugal filter in the food processing industry, where it comes into contact with acidic media and operates at high speeds. Previously, using 440C stainless steel and hard alloys yielded unsatisfactory results. Since 2017, after adopting components made from cobalt alloy welding pieces provided by our company, the equipment's performance has significantly improved.
The application of cobalt alloy welding pieces in centrifugal filters has extended the service life of equipment components, reduced replacement frequency, and enhanced production continuity. It has also lowered downtime maintenance costs caused by equipment failures and improved the company's economic efficiency. Simultaneously, its safety performance meets the production requirements of specific industries and ensures product quality.