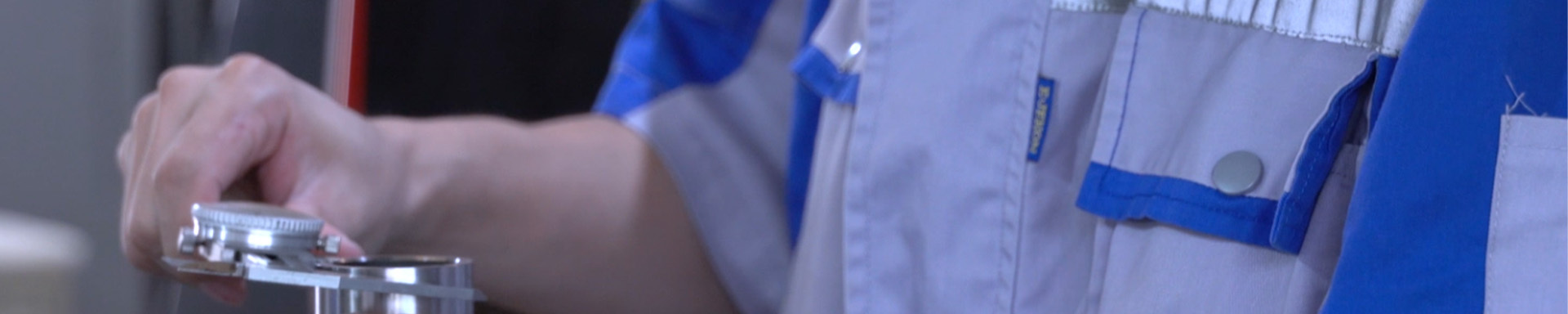
Cobalt Alloys Usage in Screw Extruders
2025-04-23 09:00As the plastics processing industry continues to increase its demands for productivity, equipment durability and environmental protection, the choice of material for extruder screws and barrels has become a core issue in technology optimization. Among many high-performance materials, cobalt alloys are gradually becoming the ideal choice for key components of plastic extruders due to their excellent wear resistance, corrosion resistance and high-temperature stability.
Cobalt Alloys Technical Characteristics
Cobalt alloy is a kind of metal alloy with cobalt, chromium and tungsten as its main components, which has the following core properties:
1. Superior abrasion resistance: its hardness can reach HRC 50-65, which is much higher than that of ordinary tool steel, and it can significantly reduce the abrasion rate of the screw and the barrel in the high-speed rotation and the friction of the material.
2. High temperature resistance: In a high temperature environment above 500 ° C, it can maintain structural stability, to avoid the deformation caused by thermal expansion.
3. Chemical resistance: excellent resistance to acidic plastic additives (such as chloride ions in PVC processing) and high temperature melt corrosion.
4. Self-lubricating: The oxide film formed on the surface of the alloy reduces direct metal-to-metal friction, reducing energy consumption and heat accumulation.
These properties make cobalt alloys particularly suitable for high-load, high-wear extrusion scenarios, such as processing of glass fiber reinforced plastics, engineering plastics (e.g., PA, PEEK), or recycled materials containing fillers.
Cobalt Alloys in Screws and Barrels
1. Integral Manufacturing
For small extruders or extruders that do not have particularly high performance requirements, it is possible to use an integral manufacturing approach, whereby screws and barrels are made directly from cobalt alloys. The advantages of this method are its simple structure and relatively easy manufacturing process, but the cost is higher.
2. Surface coating
For large-scale or more cost-sensitive extruders, surface coating can be used, the screw and barrel made of ordinary steel surface spraying or surfacing a layer of cobalt alloy coating. The advantage of this approach is that the cost is lower, and at the same time can effectively improve the screw and barrel wear resistance, corrosion resistance. Currently, the commonly used surface coating processes include plasma spraying, flame spraying, and laser cladding.
3. Set structure
In some special cases, can be used in the set structure, the cobalt alloy made of sleeve inlaid in the barrel made of ordinary steel, or cobalt alloy made of screw mandrel and ordinary steel made of screw jacket combined together. The advantage of this approach is that you can choose the right combination of materials according to the actual needs, reduce costs, and ensure the performance of the key parts.
Economic value analysis: Long-term benefits of cobalt alloys far outweigh initial costs
Although the initial material cost of cobalt alloys is higher than that of conventional steel, the overall economic value is reflected in:
Reduced downtime losses: Reduced unscheduled downtime due to screw or barrel damage improves equipment utilization.
Extended replacement cycles: Alloy reinforced parts last many times longer than conventional materials, significantly reducing the frequency of spare parts purchases.
Improvement of product quality: Stable dimensional accuracy and surface finish reduce the scrap rate.