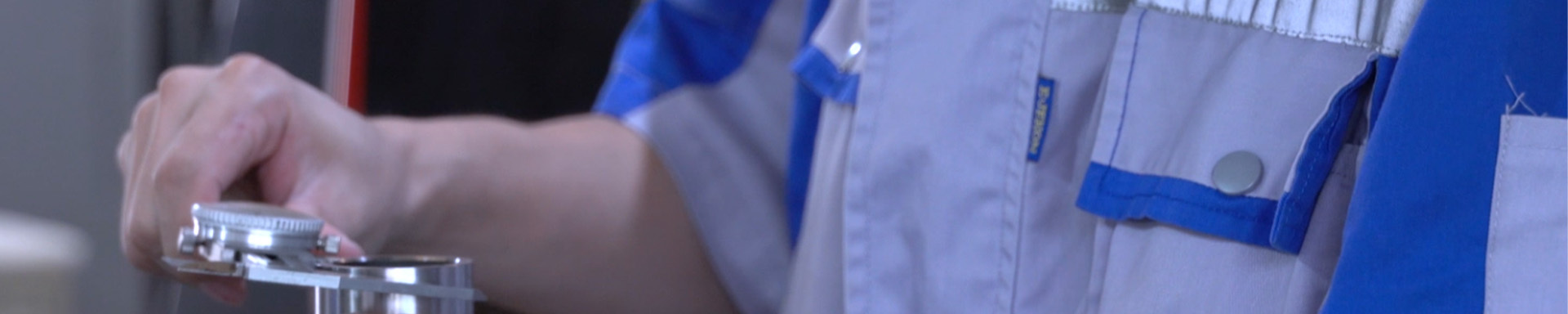
How to Choose the Right Materials for Continuous Hot Extrusion Dies for Copper?
2025-07-17 09:00In the copper processing industry, continuous hot extrusion is a core technology for producing critical profiles such as copper bars and wires, and the selection of die materials directly impacts production efficiency, product quality, and overall costs. This article will analyze the limitations of traditional mold steels from the perspective of actual production needs, detail the advantages of cobalt alloys, and provide professional guidance for enterprises in selecting materials for copper continuous hot extrusion dies through application cases.
Defining the Material Requirements for Copper Continuous Hot Extrusion
Core Requirements for Dies in the Industry
Copper bars and wires are widely used in power transmission, rail transportation, electronic devices, and other fields, with their production relying on the efficient operation of horizontal continuous hot extrusion machines. These machines process copper billets into profiles with specific cross-sections through an uninterrupted extrusion process, imposing extremely high demands on mold stability, wear resistance, and precision retention capabilities — molds must maintain consistent performance over extended production periods to ensure uniform product specifications.
Challenges in the Mold's Operating Environment
The operating environment for continuous hot extrusion of copper materials is extremely harsh: molds must continuously withstand temperatures of 500–600°C, extrusion pressures of hundreds of megapascals, and severe friction caused by the flow of copper material. Under such conditions, the mold's high-temperature hardness, wear, and thermal fatigue resistance become the core metrics for evaluating its performance. Any deficiency in these properties may lead to production interruptions or product scrap.
Shortcomings of traditional mold steels
Performance defects of H11, H13, and H21 steels
For a long time, H11, H13, and H21 hot-work mold steels have been commonly used materials for copper extrusion. However, in continuous hot extrusion scenarios, severe high-temperature decarburization occurs. At temperatures above 500°C, carbon elements on the steel surface are easily oxidized and lost, rapidly decreasing surface hardness and accelerating mold wear. When temperatures exceed 600°C, the hardness of these steels drops sharply, unable to maintain the structural strength required for extrusion, directly affecting the dimensional accuracy of the copper material. Frequent heating-cooling cycles induce alternating stresses within the mold, leading to micro-cracks forming that gradually propagate, ultimately causing premature mold failure.
Why is cobalt alloy the preferred choice for copper hot extrusion molds?
Material property advantages
ST 3, as a typical representative of cobalt-based alloys, possesses excellent high strength and toughness, high-temperature strength, and corrosion resistance, making it particularly suitable for the harsh environment of continuous hot extrusion of copper materials. At temperatures above 600°C, the ST 3 alloy maintains a hardness of HRC 40-45, gradually decreasing as temperature rises, avoiding a "cliff-like" drop, ensuring structural stability under long-term high-temperature conditions. Its wear resistance stems from strengthening the intermetallic compound inherent to the alloy rather than from carbides. As a result, its wear resistance under high-temperature friction conditions is 3-5 times that of H13 steel, effectively resisting surface wear caused by copper material flow. Cobalt-based alloys can withstand frequent temperature fluctuations, reducing the occurrence of thermal stress cracks and significantly extending the stable operating cycle of the mold.
Indian Customer Case Study
An Indian copper processing company initially had significant concerns about the high cost of ST 3 alloy when selecting mold materials. We formed a dedicated team to intervene in the mold design process: through 3D modeling, we optimized the mold runner structure, reduced the material thickness in the core working areas, and adopted a process combining ST3 and H13 for hot assembly, thereby decreasing cobalt alloy material usage while maintaining strength.
After testing the optimized ST 3 alloy mold, the customer saw a significant improvement in production efficiency. Although the cost per mold increased, the company achieved overall cost savings.
Selecting the right mold material to enhance copper production efficiency
Efficient production of copper materials through continuous hot extrusion relies on high-performance mold materials. The performance limitations of traditional mold steels in high-temperature, high-wear environments have become a bottleneck constraining industry development. Cobalt alloys offer an ideal solution to this challenge with their excellent red hardness, wear resistance, and thermal fatigue resistance.
If you face issues such as short mold life or unstable production, please get in touch with us for a customized solution.